Fasteners and Machining: Incorporating Accuracy and Stamina in Production
Fasteners and Machining: Incorporating Accuracy and Stamina in Production
Blog Article
Navigating the Globe of Fasteners and Machining: Strategies for Accuracy and Rate
In the intricate realm of fasteners and machining, the pursuit for precision and rate is a perpetual challenge that demands precise interest to detail and tactical preparation. From understanding the diverse array of fastener kinds to picking optimum products that can hold up against strenuous demands, each action in the process plays an essential function in attaining the preferred end result.
Understanding Bolt Kind
When picking bolts for a project, comprehending the various kinds available is essential for guaranteeing optimum performance and dependability. Bolts come in a vast array of types, each designed for details applications and needs. Bolts are used with nuts to hold materials together, while screws are versatile bolts that can be utilized with or without a nut, depending upon the application. Nuts, on the other hand, are inside threaded fasteners that friend with screws or screws, providing a safe and secure hold. Washing machines are vital for distributing the lots of the fastener and protecting against damage to the product being attached. Additionally, rivets are irreversible fasteners that are ideal for applications where disassembly is not called for. Understanding the distinctions between these bolt types is crucial for selecting the right one for the job, guaranteeing that the connection is strong, resilient, and reputable. By selecting the proper fastener type, you can maximize the performance and long life of your project - Fasteners and Machining.
Picking the Right Materials
Comprehending the relevance of selecting the best products is extremely important in guaranteeing the ideal efficiency and integrity of the selected bolt kinds discussed previously. When it involves bolts and machining applications, the product selection plays a vital duty in determining the overall strength, toughness, deterioration resistance, and compatibility with the desired environment. Different materials provide varying homes that can substantially affect the efficiency of the bolts.
Typical materials made use of for fasteners consist of steel, stainless steel, titanium, light weight aluminum, and brass, each having its unique toughness and weaknesses. Steel is renowned for its high strength and longevity, making it suitable for a large range of applications. Selecting the appropriate material entails thinking about variables such as stamina needs, environmental problems, and budget constraints to make certain the desired efficiency and long life of the fasteners.
Accuracy Machining Techniques
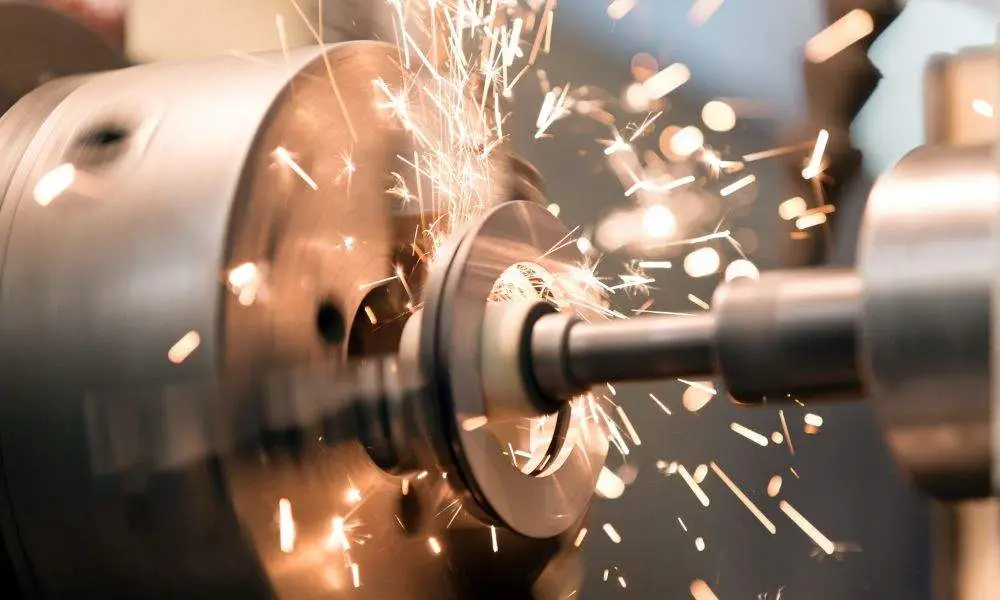
In addition to CNC machining, various other precision methods like grinding, turning, milling, and exploration play important functions in bolt production. Grinding aids achieve great surface coatings and limited dimensional tolerances, while transforming is frequently utilized to develop cylindrical elements with specific sizes. Milling and boring procedures are essential for shaping and creating holes in bolts, guaranteeing they fulfill exact requirements and function properly.
Enhancing Rate and Efficiency
To enhance bolt production procedures, it is important to enhance procedures and apply efficient techniques that match accuracy machining strategies. One key method for enhancing speed and effectiveness is the application of lean production concepts. By lowering waste and concentrating on continual renovation, lean methods assist enhance and get rid of traffic jams workflow. Additionally, purchasing automation technologies can substantially improve manufacturing rate. Automated systems can manage repeated jobs with precision and speed, enabling workers to focus on more complex and value-added tasks. Taking On Just-In-Time (JIT) supply monitoring can additionally boost performance by ensuring that the appropriate products are offered at the ideal time, reducing excess inventory and reducing preparations. Promoting a culture of cooperation and communication among group members can enhance total effectiveness by promoting openness, problem-solving, click site and innovation. By incorporating these methods, producers can achieve an equilibrium between rate and precision, ultimately enhancing their one-upmanship in the fastener market.
High Quality Control Procedures
Executing strenuous quality control steps is critical in guaranteeing the integrity and uniformity of fastener items in the manufacturing process. Quality assurance steps incorporate different phases, beginning with the selection of resources to the final examination of the completed bolts. One basic aspect of quality control is carrying out comprehensive product examinations to validate compliance with specifications. This includes examining variables such as product composition, stamina, and sturdiness to ensure that the fasteners meet market requirements. Furthermore, checking the machining refines is vital to promote dimensional precision and surface coating top quality. Using sophisticated innovation, such as automated inspection systems and accuracy measuring devices, can improve the precision and effectiveness of quality assurance procedures.
Regular calibration of devices and equipment is critical to maintain uniformity find here in manufacturing and guarantee that bolts fulfill the necessary resistances. Executing strict procedures for recognizing and resolving non-conformities or defects is vital in protecting against substandard items from getting in the market. By establishing a detailed top quality control framework, producers can maintain the online reputation of their brand and deliver bolts that meet the highest requirements of efficiency and longevity.
Conclusion
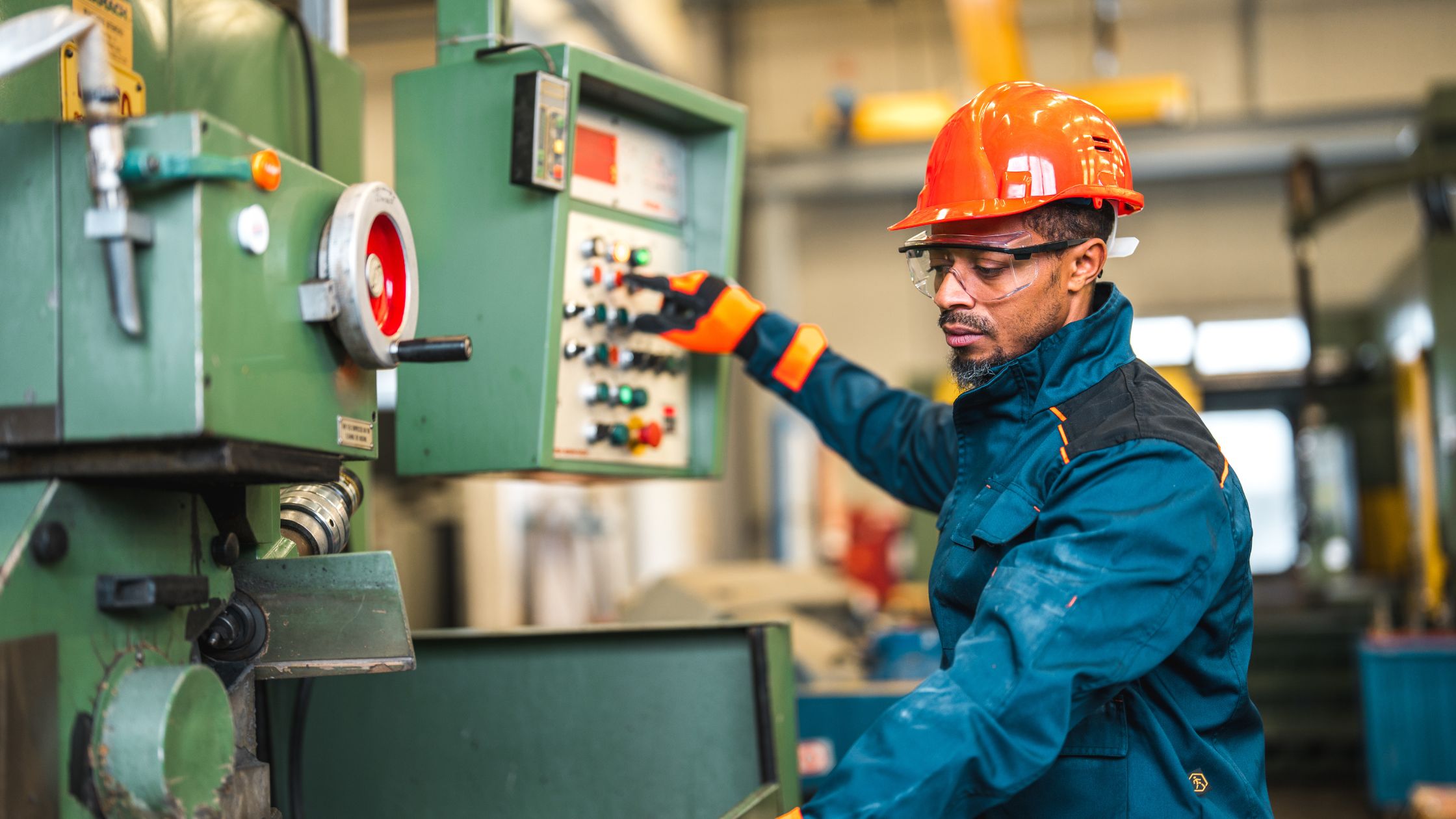
In the intricate realm of fasteners and machining, the quest for precision and rate is a continuous obstacle that requires careful image source interest to detail and calculated planning. When it comes to fasteners and machining applications, the material selection plays an essential role in identifying the general strength, sturdiness, corrosion resistance, and compatibility with the designated environment. Precision machining entails numerous sophisticated techniques that make certain the limited resistances and specs required for fasteners.In enhancement to CNC machining, other precision strategies like grinding, transforming, milling, and boring play vital functions in fastener manufacturing.To maximize fastener production procedures, it is necessary to enhance operations and apply reliable methods that match precision machining strategies.
Report this page